早稲田応用化学会・第20回交流会講演会の報告(速報)
日時 :2012年3月17日(土)15:30〜17:25 引き続き カフェテリア馬車道で懇親会17:35〜18:45
場所 :55号館 大会議室
講師 :小田切 信之氏
- 1979年応化卒(新29回生、篠原研)、1981年修士課程修了、同年(株)東レ株式会社入社、
- 現在、東レ株式会社 ACM技術部長(炭素繊維複合材料関連技術プロジェクトの統括・運営
【注】ACM:Advanced Composites Material (先進複合材料)
演題 :『化学の力が生み出した炭素繊維複合材料(CFRP)と現代社会への貢献』
― ボーイング787用材料開発を中心として ―
(画像をクリックすると拡大表示されます)
下井交流委員長の司会のもと、河村応用化学会会長の挨拶、大学・東レで演者の先輩でもある現理化学研究所監事の魚森昌彦氏より東レの事業紹介および研究開発とマーケッティングが一体となって787にspec inした今回のサクセスストーリー概略を紹介頂いた。これに続き、教員・OB ・一般74名、学生47名、合計121名(受付ベース)の聴衆を対象に講演が始まった。
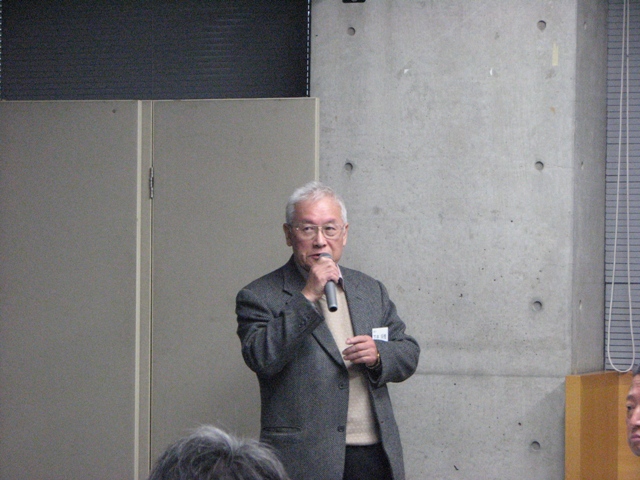
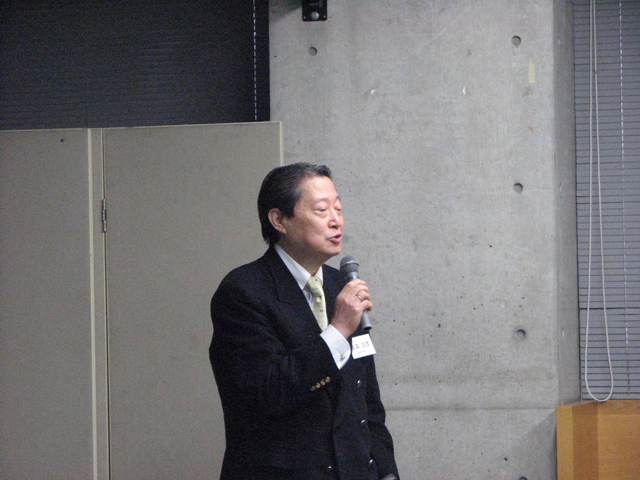
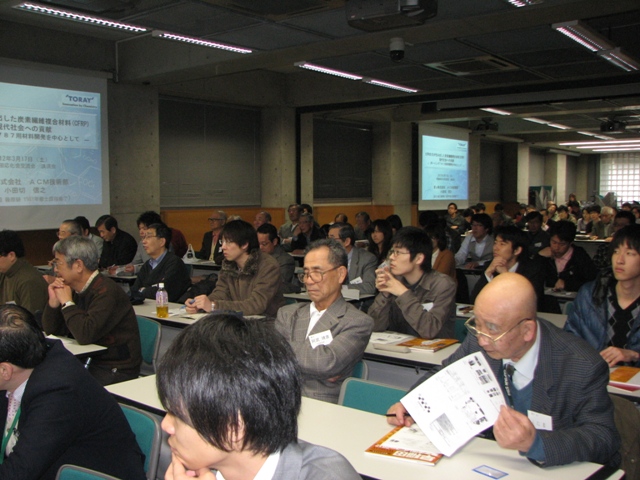
小田切信之氏の講演要旨
- 本講演全般を通じて演者は、手品みたいなことが出来る化学の力を強調し、特に若い世代の参加者をエンカレッジするとともに参加者全員に化学の魅力をメッセージし続けられた。
- 入社時からほとんどを炭素繊維研究開発や関連業務に係わっている演者の今までの略歴を紹介した後、東レの事業について、「Green Innovation」を事業戦略のkey wordとして資源を集中していること、現在3つのセグメントがあることを簡単に説明した。3つのセグメントは、一つは基幹事業であり、繊維やプラステックを対象としていること、二つ目に戦略的拡大事業があり、情報通信分野および炭素繊維が対象で、「Green Innovation」のkey technologyであり利益率の高い炭素繊維事業は将来の東レの基幹として期待されていること、三つ目には重点育成事業があり、環境エンジニアリング、ライフサイエンスを対象としていることを説明した。
- 炭素繊維は、髪の毛が50μmほどの太さに対して5μmほどの太さであることを示し、専門外の参加者に炭素繊維の具体的なイメージを与えた。さらに炭素繊維の用途別重要、地域別需要の経時での増加を示し、将来の成長性を示唆するとともに1879年のエジソンの電球のフィラメントから始まる炭素繊維開発の歴史をまとめた。同時に71年にゴルフシャフト・釣り竿に活用したときから、東レ経営陣はブレないで一貫して、この素材は必ず社会の役に立つという信念のもと基幹産業への活用を目標として忍耐強く投資を継続し、経営の意志を示してきたことも現在のサクセスストーリーの大きな要因でもあることを強調した。
- 炭素繊維の特徴としては、軽いこと、強いことがあるが、強度および弾性率を比重で割った比強度、比弾性率の二軸でプロットすると、アルミ合金、チタン合金はもとよりガラス繊維コンポジットやケプラーに代表されるアラミド繊維より圧倒的に高い領域に炭素繊維は位置する。これがアドバンスと呼んでいる所以でもある。
- その合成方法を簡単にまとめると、まずポリアクリロニトリルを200℃〜300℃でじっくりと加熱することでアメ色の耐炎化糸とする。その後1000℃〜3000℃で不活性雰囲気のなかで焼成することでグラファイト構造をつくり、油剤によるサイジング処理をして炭素繊維となる。
- 炭素繊維としての最も大きな特徴は軽くて強いことであるが、破壊は、破断面を電子顕微鏡等で観察することで繊維をつくる時のdefect(欠点)があることによって生起することがわかってきた。高強度化の極限を追求する課程を時間軸で振り返るとミクロンサイズ、サブミクロンサイズそしてナノサイズのdefectを克服したことでそれぞれの時点で不連続に強度を上げていった極限へのチャレンジの歴史といえる。しかしながら理論値はまだまだ10倍以上先にあるので今後とも挑戦し続ける必要がある。
- 同様に高弾性率の極限を追求する課程は、炭素繊維を構成しているグラファイトの配向制御の歴史であった。これも80%、95%とorientationを上げると不連続に弾性率も向上した。すでに現時点では理論値の7割程度に近づいてきているので非常に辛い研究開発ではあるが、世界のトップを走り続ける為にはより理論値に近づけるべく日々チャレンジしていかねばならないと考えている。
- 炭素繊維メーカーの消長を振り返ってみると、東レは71年から参入しているが、70年代80年代に欧米、アジアの各社が参入してきたが、ほとんど撤退や売却または規模縮小をしている。その中で東レを始めとして、東邦テナックス、三菱レイヨン等日本の会社が健闘していて、世界でシェアの約7割を制しており日本の技術が世界をリードしていて誇れることである。
- 東レはEU市場、US市場、日本・アジア市場等の最大消費地に最適配置し、それぞれに研究開発拠点も有するグローバルな研究、生産体制としている。すなわちアクリル繊維、炭素繊維、プリプレグ、コンポジットそれぞれの生産供給をグローバルに生産拠点を垂直にインテグレートして世界のお客様の重要に答える体制を構築している。
- 炭素繊維は、そのもの自体(ボビン)、クロス、プリプレグ、チョップド等の製品形態・成型法で、それぞれ、圧力容器、自動車・自転車・船舶、航空機・ゴルフシャフト、パソコン等に活用されている。
- 航空機メーカーは、ボーイングとエアバスでシェアを2分しているといえるが、ボーイング社の民間航空機におけるコンポジット使用比率拡大の歴史を見てみると、80年代後半には7%であったものが、90年代後半では777で12%に上がり、そして昨年ついに787では50%の使用率を達成した。
- 航空機への使用比率を飛躍的に上げるためには、壊れると飛行が継続できなくなる一次構造部材に本素材を活用する必要があるが、炭素繊維複合材料(CFRP)の場合はブレークスルーしなくてはならないポイントは、損傷許容設計であった。すなわち飛行中に雹、飛び石、保守点検用工具などによる衝撃を受けた時、強度の低下が許容範囲にあるかどうかが重要であった。一般にアルミ合金の場合、衝撃エネルギーに対して衝撃後の残存圧縮強度はさほど低下しないが、炭素繊維複合材料の場合一定エネルギーを超えると急激に低下してしまう。これば信頼性の低下となり、人の命に係る致命的な欠点であった。
- この課題のブレークスルーに演者らは何回も壁にぶつかったが、結論としては、プリプレグをもう一段複合化することで解決することができた。具体的には、プリプレグマトリックス樹脂であるエポキシ樹脂に高靭性を有するポリアミド系熱可塑樹脂粒子を均一に配置した。このことで衝撃を受けた時、広い範囲に広がっていたクラックが高靭性粒子によって衝撃エネルギーが吸収されることでクラックの進展を抑制することができた。
- 東レ技術の粋を集約して開発した炭素繊維プリプレグを活用した787のメリットは、軽量化-燃費向上、耐久性-メンテナンスコスト低減、高強度-窓の大型化、耐腐食性-機内湿度アップ、高強度/耐疲労特性-機内気圧向上(富士山3合目までの気圧もOKとなる)等があり787のセールスポイントとなっている。
- 787のサプライチェーンも世界一流の素材、加工技術をもとめて世界中に広がっていることも本事例の特徴でもある。東レはそれらに全て関与している。また供給力確保という観点からも異なる場所で複数の施設を整備した。材料メーカーとしてそれを短く、在庫をそれぞれが持たず高速でまわす工夫もしている。
- またより効率的に低コストの製造技術開発も東レで行っている、具体的には、A-VaRTM (Advanced-Vacuum assisted Resin Transfer Molding)成型技術開発がそれである。従来6気圧の大きなオートクレーブを用いた処理が必要だったものを、マトリックス樹脂設計に化学の粋を込めて1気圧での成型を可能にした。
- さらにエアバスへの適用予定やその他の応用例として新幹線や自動車への活用、またそれらがCO2削減にも大きく寄与することも具体的な数字で示すこともできる。
- エネルギー関連分野への活用や水素等の圧力容器、炭素繊維コア電線、船舶、土木・建築、医療機器等への活用例を足早に紹介し、東レ複合材料の将来展望のまとめの図で首題に関する講演は終了した。
- 講演を終えるにあたり、これから化学によって立とうとしている学生へ新しい価値を生み出してそれを世の中に送り出す「事業化ということ」のポイントを示した。化学の力を用い基礎研究でブレークスルーをすることで0を1にできること、生産技術、プロセス開発で1を100にする重要性、事業として成立させるために約束した品質を約束した数量約束した納期で供給することが重要であること、企業の各部門の総力結集が重要であることを示した。
- これから化学を武器に生きていこうとする場合に大切なことを最後に山に例えて学生に対してまとめた。まず裾野を広くする必要があり、それは現在大学で勉強していることでしっかり知識を蓄積することであること、その上に精神力が必要となる。さらにその上に「脳みそ力」が大切である。これは、現場で現物を直視すること、問題の本質を見抜くこと、徹底的に考え抜くこと、安易な答えを出さないこと、本当か常に疑うこと、粘りあきらめないこと、等である。世の中には頭の良い人は多いが、頭の強い人は少ない。是非頭を鍛えて強くしていって下さい。
質疑応答
講演終了後時間の制約があったため、公式には3つの質疑応答しかできなかったが懇親会、2次会と延々と質疑応答が続いた。
- Q1;航空機への採用はハードルの高くそれを成し遂げられたと思うが、それを目標としたのは何時の時点か、一般に良いものだけでは成功には至らないと思うが押す人、引っ張る人を如何に見つけたのか、LCAに関して金属と比較してどうか、リサイクルできる金属と比べて不利はないか。
A1:経営陣は70年代から強い意志決定をしていた。自分も入社直後の80年前半で同僚と議論し2000年に航空機に65%活用という夢をレポートとして提出している。本事例では押す人、引っ張る人はボーイング社であった。またkick off customerとしてANAがつき、2003年に50機発注したのも大きく寄与した。またLCAに関して炭素繊維は、金属と違いリサイクルは出来ないが最後に燃焼させることも織り込んで数値は計算している。
- Q2;航空機のジェットエンジン部分は1400℃にも達するがCFRPの耐熱温度を教えてほしい。
A2;炭素繊維自体では2000℃近くまでもつが、マトリックス樹脂としてエポキシ樹脂の場合は200℃程度となる。しかも水を吸収するとTgが下がりもっと低下する。今回活用した部材のspecは十分に水を吸収させた条件下82℃で強度を保つこととなっている。より耐熱性を求められる部材は、CFRM(メタル)を活用する必要がある。
- Q3;炭素繊維の表面処理に関して、PAN系炭素繊維のメリット、コストダウンの可能性について教えてほしい。
A3;表面処理は必須である、それぞれの用途で最適化している。電解処理でどの官能基を残しその密度をどうするかが重要である。その後サイジング剤処理を行う。PAN系に比較してピッチ系原料は安いがその後の加工コストが高くなる、一方PAN系は年々使用量の増加もありコストダウンしてアラミド繊維と同等となってきている。CFRPのコストダウンに関しては、成型コストを下げ製造サイクルを速くすることが一番コストダウンに寄与すると考える。
講演所感
今回は、早稲田大学「出る杭プログラム」から高校生の参加や一般企業からのOB以外の方の参加もあり、グローバルN0.1の技術に対する興味の大きさを伺う事ができた。例年になく外は大変寒い一日であったが、講演会場、懇親会場は演者および参加者の熱意に溢れていた。演者が何回か強調された「化学の力」を参加者一同が確信することができる有意義でかつ参加者全員が元気になれる講演会であった。優れた講演は、聴取者それぞれが有する能力、経験、興味に応じて個別にメッセージを受け取ることが出来ると考えるが、今回はまさにそのような講演であった。それをまとめることに若干の躊躇を覚えつつ拙文とさせて頂いたことを付記しておく。
<懇親会>
中川交流委員司会のもと、冒頭、菅原主任教授から開会の挨拶に続き、同門の西出教授も急遽駆けつけて乾杯のご発声と挨拶を頂いたのち懇親会が開始され多くの聴講者が参加した。懇親会では休み中にも拘らず低学年の学部生の参加も目立ち、積極的に講師との交流を求めた為、小田切氏は飲食を取ることがほとんどできなかったほどであった。「化学の力」の魅力およびそれが世の中を変える力となることを実感することができ、教員・OB・学生それぞれとの絆を深めることが出来た講演会であった。最後に小田切氏より挨拶を頂き、学生交流会の蒲ヶ原大輝君の一本締め、平沢教授の挨拶で閉会となった。
(文責:中川善行、河野善行 写真:広報委員会)
注)講演録は応用化学会報来秋号に掲載される予定です。
スナップ写真集は → こちら